【设备零故障管理】是忽悠人的空头概念吗?
发布时间:2016-12-03来源:装备保障管理网 编辑:将军

【设备零故障管理】是忽悠人的空头概念吗?
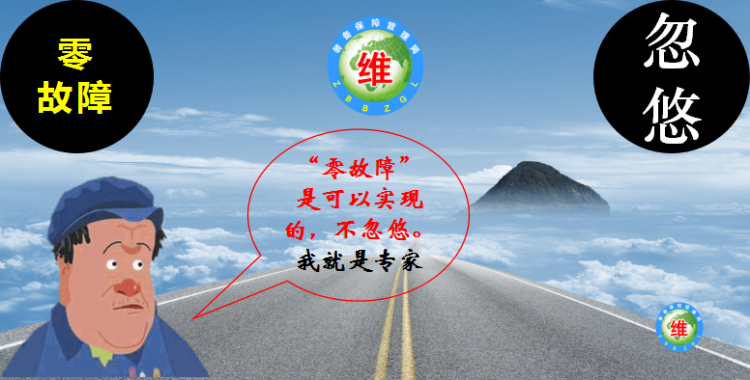
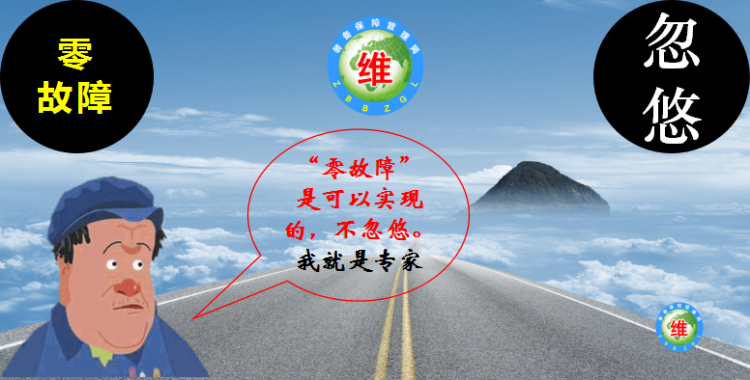
前几天在企业里,跟设备管理工作者聊天时,一设备主管言道:零故障是忽悠人的空头概念,是一些大神创造的词语,我们根本达不到。
“零故障”到底是个什么东西,今天笔者参考网络资料、专业书籍和自己的见解总结一下予以解答,敬请企业管理工作组拍砖头,大神绕行:
“零故障”作为一种工作思路,不是说绝对没有故障或故障为0,而是指要以“故障为0”作为设备管理工作的终极目标,通过趋“0”地努力,达到“一”(一次做对)的完美。
地球上搞设备管理的人都知道,日常设备管理工作中,不可能消除所有设备故障的异常因素,也是不现实不切合实际的,既然我们不能消除所有的问题让设备故障为0,我们可以将“0故障”思维融入我们具体的工作中,致力于第一次就把事情做对或防止第二次范同样的错误,并集中所有有价值资源消除最头疼的、多发的重复发生的故障,并统筹做好预防性维修和预知性维修的工作,这样装备运行状态才能可控,才能实现装备价值的最大化。
但是“零故障”是现代企业全员设备管理的目标,同时也是设备管理者追求的方向,在全员设备管理的基础上采取加强设备前半生管理、建立与之相应的设备维修策略、强化备件管理等一系列措施完善设备管理体系,推行设备“零故障”管理理念,并取得阶段性成效。
如何达到我们的目标“零故障”呢
一、明确设备“零故障”管理实施背景
设备管理工作是一个系统工程,需要积累、借鉴,更需要创新。国内企业设备管理工作取得了很大的改观,设备管理水平得到了不断的提高,现场的事故故障明显减少,但距离设备精细化管理目标还有较大差距,设备运行依然不够稳定,时而故障集中爆发,时而又运行较为平稳,波动较大,设备运行不能得到很好受控。如何才能保持设备的稳定运行成为设备管理的一道难题。
要解决这些问题,在设备管理理念上需要不断创新,设备“零故障”运行管理是全员设备管理过程中凝炼出来的一种管理理念,是全员设备管理的终极目标,从管理过程来看,是所有与设备有关的操作、维护、管理人员在对日常设备运行状态了解、认知、分析的基础上,力求稳定运行的管理,设备“零故障”运行管理是经过实践检验且行之有效的设备管理方法和手段,是众多设备管理人追求的目标,也是现代企业综合设备管理的要求。
二、明确目标及做法
1、设备“零故障”运行管理的内涵
设备只要运转就会出现故障,就像人在日常生活中会生病一样。这句话表面上看似正确,因为设备运转就会伴随着磨损、振动、发热、腐蚀、疲劳等等物理现象的产生,如果不及时消除或改善这些物理现象,最终会因此导致设备的某个部件出现故障,但我们从“故障”的语源来分析,“故障”是“人故意使设备产生障碍的”。因此,改变我们的思维及行动,设备就能实现零故障,要从“设备必然会产生故障”的观念转变为“不让设备产生故障”,只要我们去关心、爱护设备,加强设备的基础保养,及时消除各种隐患,设备是可以达到“零故障”运行的。
设备“零故障”运行管理是以“零”为目标,全力杜绝设备故障发生、维持高效、稳定的生产秩序而实施的一系列管理过程,虽然它的管理目标是“零”概念,但它不是目标效果管理,而是过程管理,是通过一系列有效的过程管理,向零概念推进,经过不断螺旋上升,直至可以使设备故障减少到接近于“零”的程度。
2、设备“零故障”运行管理的具体做法
设备“零故障”运行管理是一个系统性的管理目标,设备运行“零故障”没有捷径可走,还得从基础开始,扎实做好设备维修管理工作的每一个环节,充分掌控设备运行规律,及时有效地消除设备运行过程中产生的各种隐患,保持设备始终能够在合适的工况环境下稳定运行。
3、规范现场作业行为
一方面是提高人人参与设备管理的热情,另一方面对现场设备进行分析,制定出适用的培训计划,对职工进行技术和技能的培训,让他们明白设备的机理,懂得规范的做法和如何正确处理突发问题。并建立一套行之有效的检查监督体系,坚持开展设备经济运行评价工作,从而与规范作业一起形成一套完整的现场设备管理体系,这是实现设备“零故障”运行管理的前提条件,否则,盲目地推行设备“零故障”管理只是一句空话。
4、加强设备的前半生管理
设备前半生管理是“零故障”运行管理的第一道屏障,如果工程和生产脱节将导致设备投入运行后问题较多,增加后期的运行成本。
5、建立与之相应的设备维修策略
设备的维修策略就是要解决“何时修,如何修”的问题。合理的设备维修策略应是以预防性维修为主,辅之以状态维修,同时实施以综合经济效益为中心的多种维修方式并存的设备维修策略,比如:对非主线简单设备或备用设备采用事后维修策略,对生产主线关键、重要设备采用主动改善维修策略,对故障多、难维修的设备采用预防维修策略等,设备管理部门根据实际情况制订、完善了维修策略,对所有设备进行分类并建立各类设备的检修模型并不断进行优化,检修周期与设备实际状况有机结合,采取策略逐步延长检修周期,避免设备的过修和成本的浪费。
6、强化备件管理
备件管理在设备管理过程中占相当大的比重,如何降低库存、确保备品备件的及时供应、确保备品备件的质量等,是制约设备“零故障”运行管理的一个难题,针对存在的问题,企业应对现有设备按照设备分类的原则,进一步对部件、零件进行分类,按照分类对备件确定出不同的优先级别,对关键重点设备选取国内知名的产品质量较为稳定的一线大厂,确保备件质量;同时适度加大进口备件的国产化力度,在保证设备功能精度不降低的前提下,循序渐进地扩大转化范围,从而降低采购成本何采购周期,同时对关键备件的订货、制造、检验制定有效的跟踪机制,形成备件管理的闭环控制。
7、多样化设备的隐患排查
设备在运行阶段的关键是正确操作、精心维护、持久监测及适时检修,避免突发故障和意外停机。在排查时不仅要分析设备本身的问题,还必须注意电气系统、控制系统、仪表和安全装置可能存在的隐患,多专业协同作业,既讲究专业化分工的同时也讲究相互配合,特别是轧钢系统,通过多专业的协同配合,解决现场存在的诸多瓶颈问题,为生产创造了良好的设备条件。
积极开展设备状态管理,建立设备数据库,通过分析设备的技术数据和各种信息,评估设备或零部件的运行趋势,掌握其劣化趋势,判断设备或零部件的寿命周期,设备的检修频次得到了不断减少,设备的维修成本得到了有效降低。
8、领导支持是设备“零故障”管理是否成功的关键
在全员设备管理的基础上,推行“零故障”设备管理,往往需要一些先进的检测手段、检测设备,在条件允许的情况下可以辅以计算机管理。在这情况下,领导的支持就显得比较重要,如果领导层对一些检测手段的引进存在分歧,犹豫不决,是对基层设备管理者积极性的打击。所以,在推行设备“零故障”管理的过程中领导的支持是关键。
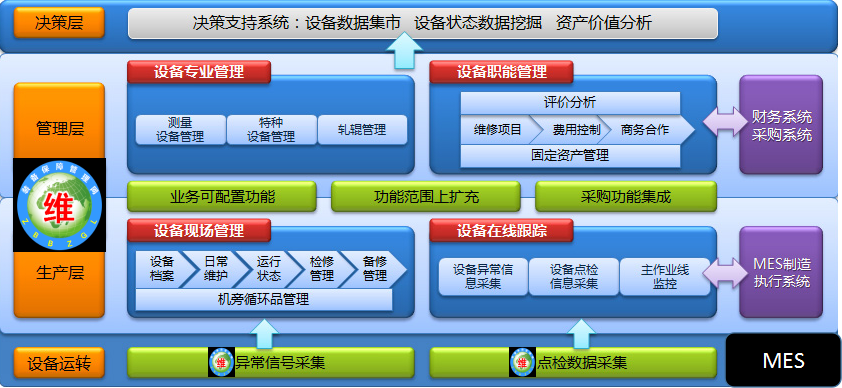
三、设备“零故障”的特点
1、坚持以预防为主的方针。
它的引导思惟因此“防”为主,改变以往以修为主的传统思惟,以最大限度地削减事故和故障发生。
2、实施全员(非口头的全员而是实际操作的全员)。
要求参加生产过程的每一位工人都要关心和参与设备的维护工作,使生产人员与设备人员融为体,成为全员的基础。
3、突出产品为中心的观念。
改变传统的“设备为生产服务以生产为中心”的腐朽观念,逐渐转变到企业盈利的发麻(产品)上来,这样既保证了的正常实行,又满足了检修要求,显露了生产与设备的统一性和协调性,真正的为企业创造价值。
4、倾向性。
依据设备状况来确定检修时刻和内容,防止过维修或久维修,其精华在于通过对设备的搜检诊断,从中发现劣化倾向性的题目,从而展望设备零部件的寿命周期,确定检修项目,提出改善措施,使设备始终处于高效,稳固运行状况。
5、目标集中。
一是削减停产检修和事后救火队,二是“经济”维修费用。
6、智能维护。
逐步建立较为完备的智能维护体系。
7、采用PDCA工作方法。
各级部门应定期召开实绩分析会,逐级提供,用数据和图表来分析故障情况、检修实验情况及维修费用行使情况,并提出改进对策和实验措施。
8、维护员工的多能化。
因为设备当代化水平和维修技术的日益发展,对维修人员的素质要求也愈来愈高,必须具有相称雄厚的实际经验、肯定的基础理论水平和较强的能力。从改变精神面貌、进步工作技有的角度倡导赓续学习的精神。
结束语:
设备“零故障”是零概念的一种,而非绝对值为零。设备“零故障”因此“零”为目标全力杜绝设备故障发生、维持高效、稳固的生产秩序而实验的一系列过程,虽然它的目标是零概念,但它不是目标效果而是过程,是通过一系列有效的过程,向零概念推进,经过赓续螺旋上升,直至可以使设备故障削减到接近于 “零”的程度。
设备“零故障”的核心是杜绝紧急维修、计划外检修、停产检修。计划外检修、紧急维修、停产检修造成的损失是无法估量的,后果也很严峻,企业价值最大化既是设备“零故障”的出发点,又是它的根本目的。
设备“零故障”是一个体系性的方法,单台设备或机组实现阶段性的零故障运行并不难,但是怎样使整个公司的生产链(产线)的影响降到最低点,则是一个复杂矛盾的题目,必须统筹综合考虑。
参考:
寿命周期评价法
西田TPM实战手册
最新设备保养制度
网络资料