设备点检管理的八大环节
发布时间:2016-12-15来源:装备保障管理网 编辑:晓刚

设备点检管理的八大环节
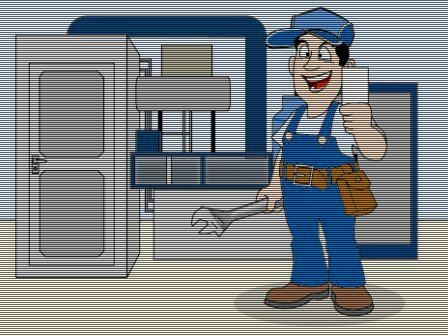
设备点检制度是一种先进的设备维护管理方法。实行设备点检制度能使设备隐患和问题得到及时发现和解决;由于检查时有明确的量化检查判定标准可以保证设备的检查和维护质量,能够早期发现设备的异常状况和劣化,有利于推广经济责任制,有利于实现计算机辅助管理。
一)点检分类
按检查作业时间间隔和内容的不同,点检工作可分为日常点检、定期点检和专项点检三类。
日常点检由设备操作人员根据规定标准,以感官为主,每日对设备的关键部位进行技术状态检查,以了解设备运行中的声响、振动、油温和油压是否正常,并进行日常保养。日常点检的结果记入日常点检表(或日常点检卡)中。
定期点检由维修人员凭感官和专用检测工具,定期对设备的技术状况进行全面检查和测定,主要测定设备的劣化程度、精度和设备的性能,目的是查明设备的缺陷和隐患,以确定修理的方案和修理的时间。点检的项目、内容和要求全部写入定期点检表中。定期点检的对象主要是重点生产设备。由于点检内容复杂,需要作业时间长和停机,所以编排定期点检计划时应与生产计划、定期维护保养计划相协调。
二)点检的主要环节
1.确定检查点
一般将设备的关键部位和薄弱环节列为检查点
2.确定点检项目
确定各检查部位(点)的检查内容。确定时要考虑必要性,还要考虑点检人员的技术水平和检测仪器的配套情况。确定后,将点检项目规范登记在检查表中。
3.制定点检的判定标准
根据制造厂家提供的技术要求和企业实践经验,制定出各检查项目的判定标准。判定标准尽可能定量化,判定标准规范化地写入检查表中。
4.确定点检周期
根据检查点在维持生产或安全上的重要性、根据生产工艺的特点,并结合设备维修经验制定点检周期。但点检周期的最后确定,需要一个摸索、试行的过程。经过对运行期的维修记录、故障和生产情况进行全面分析研究后,定出切合实际的点检周期。也可以采用理论方法先推算一个点检周期,待运行一段时间后,再作调整。理论方法是用“费用损失系数法”来计算。这个方法依据的原理是一个点检周期内单位时间的总费用(含点检费用、故障损失费用)为最小时的点检周期为最佳点检周期。
5.确定点检的方法和条件
根据点检要求,规定各检查项目采用的方法和作业条件(指是否解件、是否采用检测仪器、是否停机等)。
6.确定点检人员
即确定各类点检(指日常点检、定期点检、专项点检)的负责人和各检查点的负责人。日常点检一般由操作工人承担。
7.编制点检表
点检表是点检人员进行点检作业的依据,也是维修技术状态分析、控制和管理的重要文件。其内容有各检查点、检查项目、检查周期、检查方法、检查判定标准等。
8.做好点检记录
进行点检作业时应做好记录,以便研究分析和及时处理。