电气自动化设备管理问题探讨
发布时间:2017-01-05来源:互联网 编辑:秩名

电气自动化设备管理问题探讨
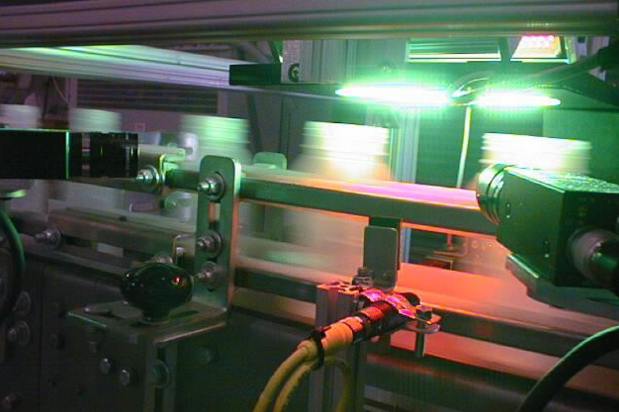
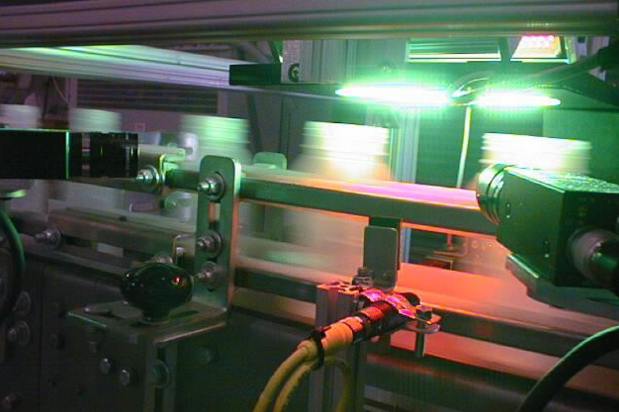
【摘要】本文介绍了利用FCS中的Profibus-DP总线实现电气设备智能管理控制系统,通过无扰切换电路设计、现场设备的数据采集、集中控制、设备管理等,使得系统的可维护性增强,减轻了生产操作的难度和强度,通过在实际中的应用,展示出FCS的优越性。
FCS现场总线是连接控制设备与上层自动化控制设备之间的双向串行链路,以其结构和布线简单、数字传输准确可靠、现场信息丰富等特点,在工厂自动化控制中得到越来越广泛的应用。它的全数字化、双向传输、多点通讯,逐步取代之前在工业中广泛应用的DCS集散控制系统。
本文采用的是其中的Profibus-DP标准,它是一种用于工厂自动化车间级监控和现场设备层数据通信与控制的现场总线技术。可实现现场设备层到车间级监控的分散式数字控制和现场通信网络,为实现工厂综合自动化和现场工艺设备智能化提供了可行的解决方案。
1.设备控制与管理
本文的工艺设备主要分为三类,一类是只需要起停控制的设备,包括除尘器、皮带运输机、搅拌电机等。控制目的是保证正常顺序开停车,以及故障或非正常状况下的连锁停车。另一类是需要调速的设备,包括泵类、风机类、给料机等设备。控制目的是参与到液位、流量、压力等的闭环控制中,以保持运行工况的稳定性。第三类是自成系统的设备,比如破碎机、球磨机、陶瓷过滤机等。这类设备相对较为独立,其信息主要是用于监测,或加入少量的控制。
对于前两类设备,与之相连的直接控制设备是变频器、软起动器、马达保护器等控制器。这些控制器接收PLC通过DP总线发出的指令,同时又将设备运行或故障信息反馈给PLC,并在上位机监控画面显示这些状态。上位机画面包含有丰富的信息,包括设备起停操作界面、运行状态信息、趋势曲线等,通过对数据库信息进行统计分析、处理,还可以在上位机中得到生产设备的历史曲线、台时、整机效率计算,电量水量统计等,实现工厂过程数据可视化及设备管理。不难看出,设备控制顺序是上位机—PLC—控制器—现场设备。
2.控制器与现场设备
对现场设备的电气控制分为就地和总线两种方式。就地控制时,现场设备起停依赖于动力站的变频器、软起动器、马达保护器等控制器接收安装在设备近旁的就地操作箱上的起停按钮或频率给定装置发出的信号;远程控制时,设备起停则依赖于控制器通过DP总线接收的上位机画面发给PLC的指令。无论这两种哪种控制方式,PLC都可以通过DP总线读到控制器中存放的设备运行或故障状态。
就地和总线切换过程要使设备平稳的保持原有状态,这种保持,除了像软起和马达保护器这些工频运行的设备不能因转换而停车或启动外,对于正在以某个频率运行的变频设备,切换时还要维持运行频率不变,即无扰切换。由于总线控制的加入,在外部电路及参数设置方面对切换电路予以充分考虑,使得就地/总线无扰切换比用DCS方式更加可靠。
无扰切换电路设计,在没有采用FCS之前,主要通过远程就地切换继电器与主回路接触器通断的时间差,来保证远程就地切换瞬间设备启动回路或运行回路不断电。即切换过程要保证主回路接触器线圈失电、触点断开的时间,要大于切换继电器线圈得电、触点闭合的时间。FCS系统,从电路及程序上,充分考虑切换的顺畅。
以变频回路为例。总线/就地切换开关不影响就地启动继电器的动作,通过变频器运行输出继电器,以及总线/就地停止继电器,来保持给变频器的启动信号维持切换之前的状态。为了保持变频器切换前后频率不变,配合以智能操作器,此操作器可显示变频器的频率给定值SV和频率反馈值MV。无论总线还是就地,MV都对应于变频器的实际频率反馈值。SV则不同。
就地时,SV显示操作器给变频器的频率设定值;总线时,SV显示的是MV通过操作器自身变送输出的值,与此时PLC通过总线设置给变频器的频率给定值基本一致。在就地切换到总线的瞬间,PLC通过总线将频率实时数据传输给变频器作为频率给定信号;在总线切换到就地的瞬间,则是利用操作器自身的无扰切换功能,操作器接收转换信号后,瞬间将显示的SV的值输出给变频器作为给定频率,从而实现双方向的可靠的无扰切换。
3.PLC与控制器
控制器主要包括变频器、软起动器、马达保护器等。为实现总线控制,需设置控制器参数。除了基本的额定电压、频率、电流、功率因数、总线地址等的设置外,对于变频器,还需要设置起停模式(如惯性、斜坡等)、加减速时间、控制信号源、频率源等;软起动器需要设置起停模式(如电压、力矩)、升降压时间、限流倍数、保护类别、输入输出功能等;马达保护器需要设置操作模式、保护设置、控制设置等。
初始设置一般是通过控制器本身的键盘完成。也可以由PLC通过DP总线对控制器参数进行设置和修改,并对控制器的特性进行连续监测与控制。
为对不同控制方式的电机进行统一管理,PLC中设置统一的电机控制变量,包括电机控制类型、控制字、状态字、频率设定、频率反馈、电机电流、电机功率、故障代码。其中电机控制类型中显示变频器控制、软起动器控制、电机保护器控制、普通电机控制等信息。控制字中包括起停电机、故障复位。状态字包括运行/停止、总线/就地、故障、急停、合闸/分闸等信息。
频率设定和频率反馈对应于变频器,电机电流、功率、故障代码对应于所有总线控制设备。故障代码是FCS较DCS优势之处,PLC通过总线读取故障代码后,可以对现场装置进行远方诊断,快速判断故障原因,排查故障。
4.上位机与PLC
上位机与PLC的通讯,采用DAServer作为接口,DAServer根据设定时间比如1000ms来读写需要与PLC交互的数据。上位机则是以事件形式读取接口中的数据。这些数据信息的读写,需要上位机进行解码及编码,以对应到特定位,实现PLC中控制字及状态字在上位机画面的显示。
对于自成系统的如球磨机等设备,由于自身存在很完备的监控系统,通过通讯读取需要特别关注的参数以显示在画面中。如球磨机的润滑油站、离合器、慢驱电机、主电机等的状态、报警等信息,轴瓦及定子温度、油压油流、振动等信息,陶瓷过滤机的循环泵、加酸泵、真空泵等相关信息。
5.上位机与服务器
上位机与PLC之间的通讯使得画面可以获得设备运行的实时数据。如若需要生产的历史数据或关键的性能指标,则需要从服务器中获得数据。各PLC设备将总线传输的与生产密切相关的设备数据存储到服务器,上位机利用ActiveFactory分析报表工具读取服务器的历史数据,以跟踪生产信息,并对信息进行分析、计算、处理,得到生产设备的历史曲线、台时、整机效率、耗电量、用水量等。
工厂过程数据可视化后,管理人员能够在详细的数据趋势及信息基础上,采取行动优化生产过程。生成数据报表及设备管理报表,提高生产绩效。
6.总结
本文利用FCS(现场总线控制系统)中的Profibus-DP总线在工厂的实际应用,从现场设备、控制器、PLC、上位机以及服务器等方面,介绍了FCS对电气设备无扰切换控制及自动化设备管理的实现方法。
【参考文献】
[1]刘幼光,黄正.浅析设备管理存在的问题与对策[J].江西冶金,2005,(01).
[2]周万珍,高鸿斌.PLC分析与设计应用[M].北京:电子工业出版社,2004.来源:中国论文网。