离心压缩机机组启动前的调试
发布时间:2017-02-13来源:装备保障管理网 编辑:维修工

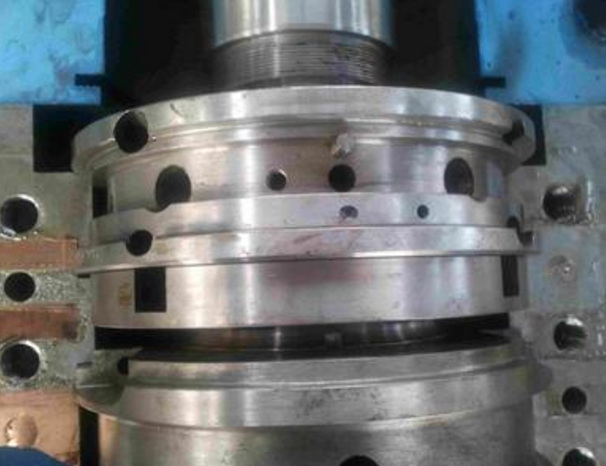
压缩机安装或检修完成后除了应对其机组各部进行严格的检查外,还要进行必要的调试,其主要目的是检查设备各系统的装置是否符合设计要求;检验和调整机组各部分的运动机构是否达到良好的跑合;
检验和调整电气、仪表自动控制系统及其附属装置的正确性与灵敏性;检验机组的油系统、冷却系统、工艺管路系统及其附属设备的严密性,并进行吹扫;
检验机组的振动,并对机组所有机械设备、电气、仪表等装置及其工艺管路的设计、制造和安装质量进行全面的考核。在试车中发现问题,查找原因,积极处理,为化工联动试车和化工投料开车做好充分的准备,创造良好条件。
二、 机组调试的要点
压缩机组在调试前应进行一些准备工作,除应达到机组运行的基本条件之外,还应包括试运人员的组织与培训、工艺管道和汽、水管道的冲洗以及压缩机和驱动机的检查与试验、油系统的清洁与检验。
(1) 试运人员的组织与培训 压缩机组在试运前应组织试运小组,定员定岗,了解、掌握机组的系统结构、特性和操作技术。编制学习试车规程、试车方案、操作规程和事故处理办法,并到生产现场进行较长时间的操作实习。试运操作人员必须进行考试,合格后方可上岗参加试运。
(2) 驱动机的单体试车试运前要对压缩机的驱动机和齿轮变速器进行严格的检查及必要的调整试验,并进行驱动机的单体试车和驱动机与齿轮变速器串联在一起的试车,经严格检验,验收合格后方可试运。
(3) 工艺管道的吹扫 初次开车前和检修管子焊接之后,必须对工艺管道进行彻底的吹扫,管内不得留存异物(如焊渣、飞溅物、废纱、砂石、氧比皮及其他机械杂物)。吹扫前在缸体入口管内加装锥形滤网,运行一段时间后再取出,以确保异物不进入气缸之内。管道内部进行酸洗后必须中和处理并用清水冲洗干净,然行干燥,以确保气体管道内绝对清洁。
(4) 油系统的清洗调试离心式压缩机组对所用润滑油、密封油和调节动力油的油质要求十分严格,不允许有较大的颗粒杂物存在,因此,在压缩机组安装完毕之后,在试车前必须对油系统进行彻底的清洗。
从已投产的机组实际情况来看,压缩机出厂后随机带来的安装在主机和油箱附近的油管路和管路附件,虽然在制造厂进行了油清洗,但由于远途运输,在油路系统内仍会存在一定的油污、铁屑、焊渣等异物;还有些需要在现场进行配制,没有进行过油清洗的,也会有焊渣、氧化物、尘土等杂质夹带在管路内。
高速运行的轴承以及调节阀、调速器在运行中即使进入少量的杂质,也会使轴承烧坏或使调节阀、调速器失灵,而危及整个机组的安全运行,因此必须对油路系统进行认真的油清洗,才能保证正常运行中油路畅通,各部件动作准确灵敏。
油路系统清洗的方法一般是在正常操作压力下,用机组运行用的油在系统内进行循环,同时使油在一定温度范围内骤冷骤热,冷却和加热的时间越短越好。
但由于油系统的油量很大,散热面积大,加上加热和冷却设备能力的限制,一般要求在1~2h内从20℃加热到80℃,保温2h,再用th降温到20℃,保温2h后再加热。
如此反复进行,造成热冲击,在冷却的同时用木制榔头按油路走向顺序敲打管壁,特别是焊缝处弯头部分,进行振动,使氧化物、焊渣等物松动脱落,以除去管内存有的杂质。
此外还可以采取别的措施,如分段冲洗;间断开停油泵及关开油路阀门,使冲洗油在管内产生漩涡流动;向管内充人氮气,使冲洗油在管路内产生紊流,以提高冲洗效果;设法提高油的流速,加大冲洗流量,为此可另外加用一个适当规格的油泵,增加管内的流量。
油的加热可以利用油箱底部的加热盘管,还可利用并联的油冷却器,使一组通热水,另一组仍通冷却水,用来交替对油进行加热或冷却,如通热水有困难,可在冷却器的进水侧接一根低压蒸汽管,在冷水中通蒸汽把水加热。
油路系统的清洗工作应分成几个步骤来进行:第一步是用机械和人工方法除去设备及管路内大量的尘土、杂物和油污等;第二步是用化学酸洗法除去设备及管路中的铁锈;第三步才是油冲洗验收。
①油路系统部件的清洗
a.油箱的清洗 先检查油箱中的保护漆,凡是质量不好的漆层都应该用喷砂的方法除去或用喷灯、液化气火焰烘烤后人工除去。但顶部漆层最好不除去,因为以后不能浸泡在漓中而容易生锈。若顶部漆层质量太差,则应除去后重涂耐油、耐温涂料。
漆层除去后应将油箱内用汽油彻底清洗干净,并用面粉团将剩余的脏物和布纤维等粘出。清理干净后,油箱内应立即灌入冲洗油,油要通过压滤机灌入,以免杂物进入,灌油量应大于60%储量,保证油泵顺利地吸油。
b.油过滤器的清洗 首先拆下油过滤器芯,然后检查内部的漆层情况,若漆层良好,只需要用汽油清洗后再用面粉团粘尽即可,否则也应进行喷砂处理。喷砂后仔细用压缩空气吹去余砂,并用面粉团粘去可能有的细小砂粒,清洗完毕后灌上冲洗油,盖上端盖。
c.油冷却器的清洗,对油冷却器应进行抽芯检查,若发现内筒壁或列管有锈蚀、污垢而需要进行化学清洗时,必须先进行脱脂。因为油冷却器内表面及列管表面一般均涂有防锈油脂,若不先行脱脂即进行酸洗,由于酸和油脂产生化学反应后生成泡沫状的污物附在筒壁内和列管上很难除尽。
脱脂后,内筒可采用酸洗或喷砂法处理,但采用喷砂法必须严格清砂。列管表面若锈蚀较为严重,则应进行化学清洗。若稍有杂物污垢等用蒸汽或压缩空气吹净即可。
油冷却器清洗完毕并重新组装后进行试压,油腔最好用油试压,水腔可用水试压,若无条件做油压试验时,油腔也可不做试压。试压完毕后油腔应注满冲洗油。
d.油蓄压器的清洗油蓄压器均为不锈钢或是内衬不锈钢的容器,只用压缩空气吹净即可。
e·高位油槽的清洗高位油槽在安装之前,就应进行喷砂处理或酸洗处理。
f.轴承箱的清洗打开轴承箱盖彻底清除杂物,并用面粉团把脏物粘掉。
g.不锈钢管的清洗所有的不锈钢管内部在安装前均应分段进行人工清理,首先用旧布在管内来回拖拉,然后用大量的热水冲洗,最后烤干。管道焊接工作采用氩弧焊,以避免内部出现焊渣,根部要焊透,以避免留存脏物。
h.碳钢管的清洗对+3in(lin=2.54cm)以上的碳钢管采用喷砂处理,喷砂结束后立即倒出余砂,并用木槌敲震,力求将砂倒净,然后用压缩空气仔细地吹净。最后在内表面涂上机油保护,管子两端设法封闭等待安装。
但要注意:喷砂以后的清砂工作必须非常严格、仔细,否则砂子带入油系统将很难除去。在内表面涂油时,注意不能用棉纱或旧布擦,否则,油系统将残存大量的纤维素。可将管路两端堵上临时薄盲板或堵上木塞,然后倒人机油并来回滚动,使油膜能覆盖所有内
表面。
对于43in以下的碳钢管,首先应观察管子内部有无大块泥土、石块,并用锤子敲击管路后将杂物倒出。然后用钢丝刷,最好是用圆盘钢丝刷绑上木杆拖刷管路内壁。经机械清理后的管路,放入酸洗槽,在酸洗液中浸泡4~5h。
取出后用清水冲洗(最好用热水)之后再放入碱洗槽中和10~20min。取出后再用水冲洗,用石蕊试纸检查水的酸碱度。当确认冲出的水已呈中性时,用蒸汽在管壁上加热,使管内水分蒸干,最后浇涂机油保护并用木塞或塑料布封闭端头。
凡原来管内有油脂保护的,都需先用蒸汽吹除脱脂,或用二氯乙烷、三氯乙烯等脱脂。
i.管路附件的清洗 油路系统中的附件,如窥视镜、管件、阀门和三通等,都要进行仔细的清洗。管路中的焊缝有未焊透的应予补焊,有焊瘤的应铲除,法兰内口焊缝应平滑饱满,以避免杂物存留在死角上。在管路焊接三通管时应先将管路切口开好,并磨好坡口后再
进行清洗,在组装时用氩弧焊打底。
②油系统的冲洗验收
a.准备工作用压滤机向油箱注入冲洗油,油位应达到最高液位。油在运到现场后应逐桶进行外观检查,并按桶数抽查10%~15%进行油的常规分析。然后在透平的调速油总管处拆开,配置临时回油管进入前轴承箱;拆下伺服马达,在动力油管开口处直接配置临时管进入轴承箱;对密封油管也应设置临时管路,使其不通过密封面进入回油管。一般不允许冲洗油进入轴承,而应配置临时管路直接进入回油管。用假瓦找正的机组,可在假瓦上钻一个直角孔,使循环油形成引路排入轴承箱。
所有冲洗用临时油管最好用碳钢管配置,并且也应事先进行化学清洗,处理干净之后方可使用。
b.第一次冲洗在第一次冲洗时可在过滤器出口和各上油管进机组处加设过滤网,在回油总管进油箱前增设过滤盒。滤网可采用120~200目的不锈钢丝网,每4h停泵拆下检查清洗一次。
第一次冲洗采用热油(60~750C)与冷油(常温)交替冲洗的方法,冲洗时间定为48h,将油系统内可能存在的杂物冲洗干净。
在第一次冲洗过程中,可用木槌频频敲击管路,特别是焊口和弯头处。在冲洗中若发现系统确已很干净,数次清洗滤网时网上已很少有杂质,也可提前结束第一阶段的冲洗工作。
在第一次冲洗结束后,视油的清洁程度而定是否更换新油。
c.第二次油冲洗和验收验收标准:油冲洗质量检查的具体标准,目前尚无统一规定,一般要求各进油滤网上肉眼看不到滤渣,或只有个别点;滤油器的临时滤芯上,每平方厘米杂质少于2~4点即可。
冲洗前应清洗过滤器芯和过滤器,并拆除过滤器出口滤网,然后将滤芯装入过滤器。机组上各油系统总管上的过滤网应清洗后装好,然后开始第二次油冲洗,并按上述标准验收。
油冲洗合格后应拆除临时管道,对未冲洗到的调节油、动力油小管(一般均为不锈钢管)用压缩空气吹净,然后将所有油系统管道复位。调速保安系统中各部分如主汽门、伺服电机、联合脱扣装置等均应拆开清洗后装上。
有的厂家将油冲洗分为两步。上述为第一步,第二步即按正常运行要求把轴承、密封和动力油系统等全部装上,让油通过所有部分,过滤器也用正式滤芯,并把润滑油、控制油的压强控制到正常操作压强,密封油达到要求的油气压差。最后以正式滤芯及各进油口滤网上肉眼见不到滤渣,油箱内的油化学分析结果无酸、无水、无灰尘为合格。
在油路系统清洗鉴定合格后,必须立即将油路管线及其有关设备进行复位,并达到设计要求状态。
压缩机组油系统的调试应具备一定的条件,如压缩机油系统不应有漏油现象;确认蓄压器内胶球完好,不漏气,不漏油;已向油系统蓄压器充入干净氮气,调速油和密封油蓄压器充入氮气的压力应符合制造厂规定。调整油冷却器阀门开度,保持供油温度在35~45℃之间。润滑油压、调速油压和密封油压应符合制造厂要求。
对压缩机组油系统进行各项试验,其中包括的联锁试验有:
①润滑油压力低报警,启动辅助油泵试验和润滑油压力低汽轮机跳闸试验;
②密封油气压差低报警,辅助油泵或辅助密封油泵自启动试验和密封油气压差低汽轮机跳闸试验;
③密封油高位油槽的液位高(低)报警试验辅助油泵(或辅助密封油泵)自启动试验,密封油高位油槽液位低汽轮机跳闸试验;
④压缩机各入口缓冲罐、段间分液罐、闪蒸槽等液位高报警及液位高汽轮机跳闸试验;
⑤主机跳闸与工艺系统的联锁保护试验等。压缩机与工艺系统的联锁试验应合格,否则压缩机不能投入运行。