智能制造时代,精益管理实战特训营
发布时间:2016-12-22来源:装备保障管理网 编辑:将军

智能制造时代,精益管理实战特训营
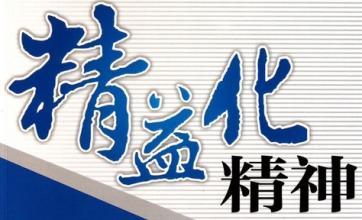
1. 劳动生产率:
1.1 劳动生产率定义:
1.2 我们的差距
2. 提高劳动生产率的战略路径
2.1 制造业的新特点倒逼战略路径
2.2 企业战略愿景倒逼战略路径
2.3 劳动生产率战略路径
3. 产业融合
3.1 产业融合是什么?
3.2 产业融合的必要性
3.3 决策模型
4. 模块化设计
4.1 理解产品的构成要素
4.2 模块定义
4.3 模块化概述
4.4 模块化设计的定义
4.5 模块化设计的益处
4.6 模块化设计步骤
4.7 模块化设计的“Y”模型
5. 模块化生产规划
5.1 模块化生产与模块化制造网络
5.2 模块化功能划分与模块化生产划分
5.3 模块化生产规划
5.4 模块化工厂的特征
5.5 模块化工厂的三种组装形式
5.6 模块总装线的工艺概念
5.7 模块化生产的益处
5.8 模块化生产规划方法概念图
6. 模块化采购
6.1 模块化采购是什么?
6.2 模块化采购的益处
6.3 采购与自制决策模型
6.4 模块全流程成本计算
7. 精益生产
7.1 什么是精益生产?
7.2 什么是精细化管理?
7.3 精益改善的逻辑。
7.4 精益转变路径
7.5 精益价值流工具。
7.6 精益知识体系
8. 自动化
8.1 自动化带来的益处
8.2 自动化的局限性
8.3 哪些动作适合自动化?
8.4 自动化评估模型
8.5 自动化项目实施的步骤。
9. 劳动力资源优化
9.1 认识浪费
9.2 人员利用率定义
9.3 人员利用率测量
9.4 制造资源管理的逻辑
9.5 人员需求计划
9.6 劳动力资源调配示意图
9.7 劳动力资源调配架构
10. 生产外包
10.1 为什么要进行生产外包?
10.2 生产外包的特点
10.3 外包的步骤
10.4 方法与工具
11 例子
2、《精益与精细化转变路线图》
1. 企业面临的挑战与机遇
1.1 企业面临的挑战
1.2 企业面临的机遇
2. 精益生产介绍
2.1 精益生产是什么?
2.2 精细化管理是什么?
2.3 从管理流程与管理系统的角度理解精益。
2.4 精益的五大原则
2.5 精益生产架构
2.6 精益构成要素与工具
2.7 消除浪费与标准化是精益的核心
2.8 精益给我们带来什么变化?
2.8.1 从研发角度看
2.8.2 从工艺角度看
2.8.3 从生产方式角度看
2.8.4 从生产计划看
2.8.5 从质量管控看
2.8.6 从人员效率看
2.8.7 从设备维护角度看
2.8.8 从工厂布置看
2.8.9 从物料供应看
2.9 精益给我们带来什么益处?
3.0 精益制造与职能制造
3.1 智能制造是什么?
3.2 智能制造的演化过程
3.3 智能制造的价值演化图
3.4 智能制造的升级逻辑
3.5 智能制造的实施路径
40. 精益实施路径
4.1 确定精益战略及实施准备
4.2 什么是改善活动
4.3 定义价值
4.4 确定新的流程
4.5 实施流动
4.6 实施拉式系统
4.7 完善生产系统
50. 个性化解决方案
5.1 儿童期企业与青年期企业的特点
5.2 企业管理升级的“五字”经。
5.3 企业的特点决定具体的实施步骤
3、《价值与浪费》
1.0 价值
1.1 什么是价值?
1.2 识别价值
1.3 价值流是什么?
1.4 公司定价习惯的改变
1.5 理解价值
1.6 一个帮助决定价值的简单工具
2.0 浪费
2.1 什么是浪费
2.2 八大浪费
2.3 过盈生产浪费
2.4 库存浪费
2.5 等待的浪费
2.6 搬运的浪费
2.7 动作的浪费
2.8 不良品修正的浪费
2.9 过度加工的浪费
2.10 智力的浪费
2.11 练习
4、《价值流管理》
1.0 关于价值流及价值流图
1.1 识别价值
1.2 价值流是什么?
1.3 价值流图是什么?
2.0 价值流图解析
2.1 价值流图分析的益处
2.2 价值流图分析步骤
2.3 解读价值流
2.4 价值流图的基本结构
2.5 价值流图的图标
2.6 数据框包含的数据
2.7 增值时间与非增值时间
3.0 价值流图绘制方法
3.1 选择一个价值流
3.2 组成一个小组
3.3 理解客户的需求
3.4 绘制主要过程流
3.5 绘制物料流
3.6 绘制信息流
3.7 计算总的生产周期TPCT
3.8 绘制精益价值流的准则
3.8.1 要按节拍生产
3.8.2 在可能的地方发展连续流
3.8.3 在连续流动无法向上游扩展处使用超市控制生产。
3.8.4 努力将顾客订单计划只发到一个生产过程
3.8.5 在定拍过程按时间均匀分多品种生产
3.9 需要考虑的几个问题
3.9.1 你想建立成品超市还是直接发运
3.9.2 哪里可以使用连续流动的过程
3.9.3 哪里需要使用超市的拉动控制上游的生产?
3.9.4 在整个生产链中,你将在哪个点计划生产?
3.9.5 在节拍控制工序,如何均衡生产不同的工序?
4. 0 绘制未来价值流图。
5. 0制定改善计划
5.1 分解价值流,识别价值环
5.2 计划制定的原则SMART原则
5.3 价值流改进的例子
60. 主要衡量指标
6.1 进料仓库到出料仓库的时间-DTD
6.2 首次合格率-FTT
6.3 综合设备效率-OEE
70. 价值流绘制的例子
5、《6S与目视化管理》
1.0 6S 活动介绍
1.1 6S起源
1.2 6S含义
1.3 6S的必要性
1.4 6S活动的展开方向
2.0 6S 活动推进方法
2.1 整理阶段
2.1.1 整理的定义
2.1.2 整理的必要性与益处
2.1.3 整理的对象
2.1.4 整理的处置
2.1.5 如何处置非必须品
2.1.6 整理的推进步骤
2.1.7 整理实施的主要方法
2.1.8 红标牌作战
2.2 整顿阶段
2.2.1 整顿的定义
2.2.2 整顿的必要性
2.2.3 整顿的步骤
2.2.4 整顿的实施方法
2.2.5 涂料作战
2.2.6 三定活动
2.2.7 整顿例子
2.2.8 整顿的技巧总结
2.3 清扫阶段
2.3.1 清扫的定义
2.3.2 清扫的必要性与益处
2.3.3 清扫的步骤与方法
2.3.4 清扫制度化
2.4 清洁阶段
2.4.1 清洁的必要性
2.4.2 清洁的目的
2.4.3 清洁的重点
2.4.4 清洁的步骤
2.5 素养阶段
2.5.1 素养的必要性
2.5.2 素养的目的
2.5.3 素养的重点
2.5.4 素养活动的内容
2.5.5 素养的实施方法
2.5.6 素养的检查点
2.6 5S总结
3.0 安全管理
3.1 安全的含义
3.2 安全的分类
3.3 事故分类
3.4 事故发生的原因
3.5 安全管理的目的
3.6 安全实施的要领
3.7 安全管理的步骤
3.8 抓好现场安全工作
4.0 如何推进6S活动
4.1 目标制定
4.2 组织保障
4.3 机制保障
4.4 职责保障
4.5 工作表单
5.0 目视化管理
5.1 什么是目视化管理
5.2 为什么要目视化管理
5.3 目视化管理的目的
5.4 目视化管理系统
5.5 目视化管理的对象
5.6 目视化管理工具
5.7 目视化管理的要点
5.8 目视化管理七要素
5.9 现场目视化活动
5.10 设备目视化管理
5.11 现场目视化管理
5.12 安全目视化管理
5.13 物流的目视化管理
5.14 目视化显示与控制
6、《kaizen活动介绍》
1.0 Kaizen活动
1.1 Kaizen 是什么?
1.2 kaizen方法
1.3 Kaizen益处
2.0 Kaizen活动步骤
2.1 选择将要改善的流程
2.1.1 选择改善流程
2.1.2 选择小组领导人
2.1.3 咨询师的角色
2.2 明确问题描述与项目目标
2.2.1 阐明
2.2.2 用SMART明确目标
2.3 组织活动
2.3.1 组织
2.3.2 选择团队
2.3.3 培训团队
2.3.4 准备(场所,装备,后勤)
2.4 实施活动
2.4.1 议程
2.4.2 团队会议
2.4.3 10大原则
2.4.4 实施第一与第二步
2.4.5 回报
2.5 评价
2.5.1 评估
2.5.2 跟踪
2.5.3 领导层评估
2.5.4 反馈与总结
8、《单元设计》
1.0 单元设计简介
2.0 重温主要的精益概念
2.1 节拍
2.2 价值与浪费
2.3 八种浪费
2.4 如何发现浪费
3.0 单元设计的基本元素
4.0 实例分享
5.0 运行模拟的生产线
6.0 施展单元设计
6.1 记录过程
6.2 重新设计生产单元
7.0 运行新的设计
8.0 管理生产单元
9、《工作防呆设计》
1.0 防呆法概述
1.1 防呆法定义
1.2 防呆的益处
2.0 失误与缺陷
2.1 失误的原因
2.2 防呆原理
2.2.1 失误的分类
2.2.2 对待失误的两种观点
2.2.3 防呆的四项基本原则
2.2.4 防呆的理念与思路
2.2.5 防呆的应用原理
2.2.5.1 断根原理
2.2.5.2 保险原理
2.2.5.3 自动原理
2.2.5.4 相符原理
2.2.5.5 顺序原理
2.2.5.6 隔离原理
2.2.5.7 复制原理
2.2.5.8 曾别原理
2.2.5.9 警告原理
2.2.5.10 缓和原理
2.2.6 防呆步骤
2.2.7 练习
10、《流动与看板》
1.0 看板管理介绍
1.1 超市与看板
1.2 什么是看板?
2.0 生产方式分类
2.1 流水线生产
2.2 拉式生产
2.3 推式生产
2.4 推式与拉式生产的区别
2.5 拉式系统的目标
2.6 拉式系统的先决条件
3.0 看板类型
4.0 看板管理机制
4.1 看板规则
4.2 two-bin 系统
4.3 信号化生产看板
4.4 看板信号
4.5 看板的计算
4.6 看板例子
4.7 实施看板的步骤
4.8 看板管理的原则
4.9 看板的量测系统
11、《单分钟换模-SMED》
1.0 单分钟换模(SMED)
1.1 什么是SMED?
1.2 为什么SMED很重要?
1.3 什么是设置时间?
1.4 降低设置时间的益处
1.5 降低设置时间的目标
2. 减少设置时间的步骤
2.1 观察记录作业现状
2.2 分离内外部设置作业
2.3 内部设置转化为外部设置
2.4 改进内外部设置
2.4.1 维护问题
2.4.2 运输搬运问题
2.4.3 设置和调整
2.4.4 工具和夹具定位
2.4.5 拧紧和紧固
2.4.6 非标准工具
2.4.7 数据输入
2.4.8 操作自动化
2.4.9 标准化
2.4.10 标识
2.4.11 定位
2.5 案例分享
12、《作业标准与标准化作业》
1.0 标准工作
1.1 标准工作是精益的基础
1.2 标准化和改善
1.3 缺少标准的影响
2.0 标准工作方法的定义,目的和益处
2.1 标准工作方法的定义
2.2 标准工作的目的
2.3 标准工作的益处
3.0 标准作业的基础
3.1 节拍
3.2 周期时间
3.3 节拍VS.周期时间
3.4 工作顺序
3.5 人员流动VS. 物料流动
3.6 标准在制品
4.0 建立标准作业
4.1 实施布局改变
4.2 实施流程改变
4.3 交叉培训
4.4 记录人员作业
4.5 平衡操作时间
4.6 平衡序列时间
4.7 完成时间
4.8 完成标准作业表单
4.8.1 时间测试表
4.8.2 生产能力表
4.8.3 作业平衡表
4.8.4 标准作业组合表
4.8.5 标准作业表
13、《班组建设与班组长管理实践》
1.0 班组文化与班组建设
1.1 班组文化
1.2 班组建设
1.2.1 组织建设
1.2.2 制度建设
2.0 班组长的角色认知
2.1 班组长的管理水平现状
2.2 班组长的地位和作用
2.2.1 班组长的产生形式
2.2.2 班组长的地位
2.2.3 班组长的重要作用
2.3 班组长的职责和权限
2.3.1 班组长的职责
2.3.2 班组长的权限
2.4 班组长的素质和技能
2.4.1 班组长的素质要求
2.4.2 班组长的技能要求
3.0 班组生产管理(上)
3.1 班前计划
3.1. 班组长在生产准备中的任务
3.2 班前交接管理
3.3 班前会议管理
3.4 生产派工
3.5 “机动部队”与“职务代理人制度”
4.0 班组生产管理(下)
4.1 班中控制
4.1.1 班组长在作业过程中应把握的内容
4.1.2 发挥班组“六大员”的作用
4.1.3 进度控制与横向协调
4.2 班后总结
4.2.1 订单完成后的总结
4.2.2 班后会的管理
5.0 班组质量管理
5.1 员工质量意识再造
5.2 质量实现“三大控制”
5.3 品管“三招半”
6.0 班组物料管理
6.1 物料分类
6.1.1 ABC物料分类
6.1.2 物料编码
6.2 在制品管理
6.2.1 在制品流动管理
6.2.2 在制品的盘点
6.3 班组与库存管理
6.3.1 仓库“黑洞”
6.3.2 仓管员的“收-管-发”
6.3.3 呆废料的处理
7.0 班组技术与工艺管理
7.1 技术管理---标准化建立与完善
7.1.1 制造现场的工作标准的制定
7.1.2 制造现场的工作标准的教育
7.1.3 制造现场的工作标准的应用
7.2 工艺管理---工艺应用与实施
7.2.1 工艺与工艺管理
7.2.2 工艺标准
7.2.3 工艺规程的执行
8.0 班组设备与工具管理
8.1 班组设备的日常“三级保养”
8.1.1 一级保养有操作人员负责
8.1.2 二级保养由班组长负责
8.1.3 三级保养由设备管理部门负责
8.2 班组日常工具管理
8.2.1 班组工具的分类
8.2.2 班组日常工具的管理
8.3 TPM
8.3.1 TPM是顺应时代的需要而发展的
8.3.2 TPM的定义
8.3.3 TPM的效果
9.0 班组人员管理
9.1 2/8 原则与ABC对员工分析
9.1.1 20%员工当中的ABC员工
9.1.2 80%员工当中的ABC员工
9.2 刚性与柔性
9.2.1 刚性-制度化
9.2.2 柔性-人性化
9.3 根据性格类型进行管理
9.3.1 指挥型员工的管理
9.3.2 关系型员工的管理
9.3.3 智力型员工的管理
9.3.4 工兵型员工的管理
10.0 班组成本管理与经济核算
10.1 要不得的成本意识
10.2 消除班组的七大浪费
10.3 班组成本的降低
10.4 经济核算透明化与可量化
10.4.1 经济指标
10.4.2 内部结算
11.0 班组现场管理与“5S”
11.1 班组现场混乱的根源
11.2 现场浪费所产生的浪费
11.3 5S的由来与6S的管理
12.0 班组长的领导艺术
12.1 了解上级的期望与了解下级的期望
12.2 以“德”服人,以“才”易人
12.3 总结
14、《共享经济在生产制造中的实践—提高制造资源的利用效率》
1.0 企业运营过程中遇到的困惑
1.1 人力资源部门在纠结什么?
1.2 员工在抱怨什么?
1.3 现实情况是什么?
1.4 真实情况是什么?
1.5 设备是有生命的
1.6 这样的场地规划我们不要
2.0 制造业的竞争终究是效率的竞争
2.1 认识浪费
2.2 企业面临的挑战
2.3 什么是生产率?
2.4 生产率管理循环
2.5 劳动生产率是什么?
2.6 我们的差距
2.7 提高生产率的战略路路经
2.8 生产率提升的价值演化图
3.0 制造资源的管理
3.0.1 制造资源管理是什么?
3.0.2 制造资源管理的内容
3.0.3 制造资源管理的逻辑
3.1. 利用率的测量与评价
3.1.1 利用率测量
3.1.2 生产要素的利用率测量
3.1.3 利用率测量与评价的意义
3.1.3 人员利用率定义
3.1.4 理解我们的工作
3.1.5 人员利用率测量
3.1.6 人员利用率评价
3.1.7 提高人员利用率的方法
3.1.8 关于产能
3.1.9 设备利用率定义
3.1.10 设备利用率量测
3.1.11 设备利用率评价
3.1.12 提高设备能力利用率方法
3.1.13 库存周转率量测
3.1.14 制造周期与在制品的关系
3.1.15 提高库存周转率的方法
3.1.16 面积产出率量测
3.1.17 提高面积产出率的方法
3.2 制造资源的需求计划
3.2.1 人员需求数量量测
3.2.2 设备需求数量量测
3.2.3 面积需求数量量测
3.3 制造资源的共享
3.3.1 关于共享经济
3.3.2 共享经济的未来
3.3.3 企业人力资源共享模型
3.3.4 人力资源共享的组织实施
3.3.5 人力资源共享的益处
3.3.6 企业人力资源共享的步骤
3.3.7 工作分类
3.3.8 培训矩阵
3.3.9 设备共享模型
3.3.10 设备共享的步骤
3.3.11 设备分类
3.3.12 规划是场地共享的基础
3.3.13 场地规划的原则
3.3.14 场地规划的模型
3.3.15 场地规划的四个视角
3.3.16 场地规划与场地共享的例子
3.3.17 其他制造资源的共享
3.3.18 制造资源共享的社会意义
4.0 回顾与问答
15、《两种IE改善手法的介绍》
1.0 IE 八大手法介绍
2.0 八大手法之一(人机配合法)
2.1 人机配合法简介
2.2 人机操作法
2.3 联合操作法
2.4 双手操作法
2.5 闲余能量分析
2.6 机器干扰研究
3.0 八大手法之一(流程法)
3.1 流程法概念/意义
3.2 流程法目的
3.3 流程法范围与作用
3.4 流程法分类与案例
3.5 流程法改善的着眼点
3.6 流程法改善的六大步骤
16、《流程改善的常用工具》
第一节 《改善工具的简介》
1.1 QC 是什么?
1.2 QC 七大手法
1.3 IE 是什么?
1.4 IE 八大手法
1.5 QC与IE改善的侧重点是什么?
1.6 课程内容安排
1.6.1 QC 手法(特性要因图,柏拉图)
1.6.2 IE 手法 (人机配合法,流程分析法,动改法,线平衡法)
第二节 《特性要因图》
2.1 特性要因图的定义
2.2 特性要因图的用途
2.3 特性要因图的绘制步骤
2.4 特性要因图的例子
2.5 课堂练习
第三节 《柏拉图》
3.1 柏拉图的定义
3.2 柏拉图的用途
3.3 柏拉图的绘制步骤
3.4 柏拉图的例子
3.5 课堂练习
第四节 《价值与浪费概述》
4.1 什么是价值
4.2 价值的流动
4.3 什么是浪费?
4.4 制造过程的浪费分析
4.5 制造过程浪费的例子
第五节 《人机配合法》
5.1 人机配合法简介
5.2 人机操作分析
5.2.1 人机操作分析图用途
5.2.2 人机操作图制作
5.2.3 人机操作图例子
5.2.4 人机操作分析步骤
5.2.5 人机操作分析改善着眼点
5.3 联合操作分析
5.3.1 联合操作图制作
5.3.2 联合操作图制作案例
5.3.3 联合操作分析步骤
5.4 课堂练习
第六节 《流程分析法》
6.1 流程法简介
6.2 流程法流程分析的种类
6.3 流程法分析的工具-流程程序图
6.4 工程分析的符号
6.5 物料型改善案例讲解
6.6 人流型改善案例讲解
6.7 流程分析改善的着眼点
6.8 流程法的六大步骤
6.9 课堂练习
第七节 《动改法》
7.1 动改法概述
7.2 动作经济原则
7.2.1 关于人体的运用
7.2.2 关于工作场所的布置与环境
7.2.3 关于工具和设备的设计
7.3 动素分析
7.3.1 动素是什么?
7.3.2 动素的分类及其符号
7.3.3 动素分析
7.3.4 动素分析的步骤
7.4 动改法案例展示
7.5 课堂练习
第八节 《线平衡法》
8.1 木桶原理和管道原理
8.2 生产线平衡的目的
8.3 线平衡法的术语
8.4 生产线平衡的步骤
8.5 生产线平衡的实战技法
8.5.1 克服瓶颈
8.5.2 正确理解三种瓶颈工站
8.5.3 瓶颈产生的原因分析
8.5.4 瓶颈改善的方向
8.5.5 瓶颈改善的方法
8.5.5.1 “ECRS”改善方法
8.5.5.2 6M分析改善法
8.6 生产线平衡常见问题
8.7 打破平衡
8.8 课堂练习