计划保全的推行步骤
发布时间:2017-05-24来源:互联网 编辑:秩名

计划保全的推行步骤
计划保全要变为可执行的方式和方法,需要将计划保全具体化和分阶段执行,使管理者有侧重点实施和管理。
一般可分为五个阶段或步骤来实施,即设备状态诊断、计划保全的编制和实施、故障解析及改良保养、计划保全的扩大、计划保全值的提升。
1、设备状态诊断和保养标准建立
只有对每台设备盼现状进行了充分的认识和把握,并根据设备的使用年限、产品特性和质量操作要点等要求,才能制定相应的保养和维护的标准、对应措施和计划,并依据维护标准长效坚持。
①设备现状和保养数据的收集
企业需要采集的保养数据包括:设备的购买时间、价格,验收的情况,平时的保养状况和加工精度情况,故障产生的时间、状况、原因及解决方法。这些数据记录得越详细,对于制定保养计划就越有救果。记录保养数据最好的方法是建立设备档案。
设备从进厂开始,直到报废都要入档,档案中除了记录设备的构造原理、设计原理、线路图、操作规程外,还要包括设备的保养记录。其来源主要是:机械设备卡、设备使用和操作说明书、润滑说明、编制的保养和检查标准等。
②保养数据的分析方法
对于设备的保养记录,应进行科学详细的分析,分析数据的规律、机器故障发生的环境、故障原因等,由此制定出合适的保养计划,从而防止故障的发生。通常要进行平均故障时间、保养月报、保养比率这几种数据的统计,如表所示。
保养数据的分析方法
2、计划保养的编制和实施
①保养计划编制
保养计划的准确性决定了保养的有效性,同时也决定了经济性。因此在编制保养计划时,应制定以设备操作者和设备维修人员夯中心的保养计划。
②实施目标管理,确定保养工作的目标
在编制了可行的保养计划后,就应该设定管理目标。策划并鼓励能使全员参与的方案,达到保养时效快、品质好和成本低的目的。
c.折中保养,即采取集中+分区的保养方式。
3、故障的解析和改良保养
①确定设备的薄弱环节
依据点检(操作者和专业人员)、巡检、设备普查、维修和监控等动态资料,寻找薄弱设备和设备薄弱环节,及时组织审理,确定当前应解决的项目,提出改进方案;设备管理部门应组织有关人员对改进方案进行审议,审定后列入检修计划;设备薄弱环节改进实施后,要进行效果考察,作出评价意见,经有关领导审阅后,存入设备档案。
凡属下列情况均属设备薄弱环节:运行中经常发生故障停机而反复处理无效的部位;运行中影响产品质量和产量的设备、部位;运行达不到小修周期要求,经常要进行计划外检修的部位(或设备);存在不安全隐患(人身及设备安全),且日常维护和简单修理无法解决的部位或设备。
②故障分析方法
专业保养人员应针对每种设备的原理、设计和构造等,确定不同的分析方法。通过专业人员向普通员工讲解,使员工了解到故障的原因,确定是多发故障、经常发生故障还是重大故障,然后找出排除故障的方法。
③防止事故的再次发生
解决了一次故障之后,怎么防止故障的再次发生,是我们要解决的首要问题。防止故障再次发生主要有五个步骤:分析和复原,分析故障原因,故障接触,制定标准,最后根据标准进行日常的管理。按照这五步就能防止故障的再次发生。
4、计划保养的扩大
①计划保养的扩大
计划保养不仅要在生产设备上实施,而且应推广到其他方面,如进行保养性提升的研究、保养的效率化的研究、制定生产历程表和保养历程表。这些规章制度的确定可以大大缩短整修的时间。
②备品备件的管理
保养维修设备需要使用大量的备品备件和易损件,在对其进行管理时,应该按照突发性和计划性进行分类管理,其管理状态将直接影响到设备维修结果,进而影响生产的进程。因此,加强对其的有效管理也是一个重要的环节。
③进行改良保养
为了改良保养,机械使用人必须把故障状态详细记录,并积极提出防止故障再发生的改善提案。机械设计人员将保养人员所提出的故障记录及改善提案作为根据、讨论内容,将机械改善为不容易故障,容易保养的机械,成为更有效率的机械。其改良保养方向:性能分析、故障分析、材料研究、设计变更、超载防纸装置、防腐防锈、操作标准建立、其他。
5、计划保全质的提升
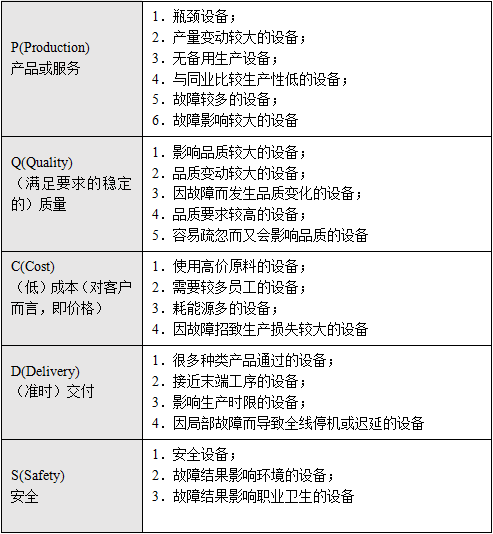