丰田的改善思想精髓,值得我们学习
发布时间:2020-07-03来源:装备保障管理网 编辑:俏电工

丰田的改善思想精髓,值得我们学习
学习TPS(丰田生产方式),我们首先接触的就是七大浪费。但是我们往往却忽视了企业中最大的一个浪费,就是企业对于人力资源的浪费。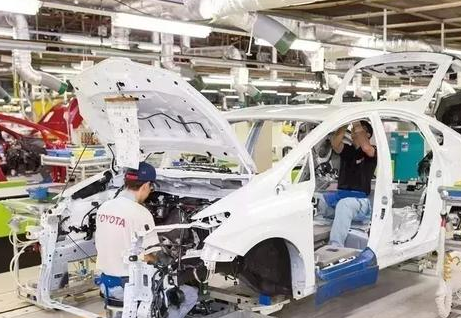
任何一个到过丰田的人,大都会被丰田的员工震撼,因为丰田的员工太不一样了,不仅工作认真,还会着了魔似的为公司贡献各种小点子,以消除工作中的浪费、降低成本。
据统计, 丰田公司1986年的合理化建议数为2648740件, 平均每人47件, 员工参加率为95%, 采用率达到了96%。自1989年以来因员工提出的合理化建议而减少的生产成本已达数亿美元, 其中仅1997年一年就减少7200万美元。可见,合理化建议活动在丰田经营管理中的作用和产生的巨大经济效益。1988年,丰田公司合理化建议的表彰金就达3亿多日元。
“不是去工作,而是去动脑,去展示自己的智慧。”
“如果你觉得工作干起来很吃力,很累人,很麻烦,,工作是一件让人难以忍受,要去思考怎样才能让自己轻松起来。”
这是丰田管理者经常说的一句话。为什么要这么说, 丰田的管理人员解释说, 生产一线的员工每天都要重复相同的工作。为了不让工作太单调, 大家想了很多办法, 尽管如此, 工作还是单调得令人生厌,让人觉得很累。在这种情况下,员工们 很容易产生“去工作真是件令人讨厌的事”的想法。
在丰田车间, 我们看到了很多日本80后男孩,把长头发夹在帽子里,快乐地工作,事实上,丰田的员工待遇, 并不比同类的其它日本公司高, 但丰田员工的忠诚度与贡献, 却是很多同类公司无法比拟的。
丰田“改善”之所以上升到魂,就在于此,丰田改善有重要的三句话:
“多提方案比提出好的方案更有价值”。
“不允许对员工的提案,用评论家的口气提出质疑”。
“没有代替方案就别轻言反对”。
有员工的智慧的发挥,才有真正的企业竞争力。丰田车工部有一个叫铃木胜康的工人,提出了一个消除座位下弹簧发出“格吱”响声的建议。很简单,就是在接头部位涂上石蜡,然后烘干,问题就解决了。这个小点子使用后客户大为满意。铃木胜康因此得到了公司10万日圆奖金,还申请了日本国内和美国专利加以保护。
如果员工对生产过程进行了深入的观察,并看到了其中的浪费, 就会满意的让员工下班。这种培训是教授员工现地现物的开始。通过培训,会使员工意识到仅凭对生产过程的初次、表面的印象并不能发现生产系统中所存在的浪费,为了真正了解生产系统中的问题,必须进行更加深入的观察。