设备零故障活动---三管三分法、助企业实现突发故障为“零”
发布时间:2023-03-22来源:装备保障管理网 编辑:装备保障管理网

〖主讲内容〗
第一篇:新时代下的现代设备管理体系构建
第一节、设备管理的根基
1、 构建设备全生命周期管理体系总体框架
2、设备管理意识-“生产负荷中没有时间停机,设备该不该停机点检”
3、设备发展的形势与挑战
4、3T底层逻辑(TPM TPS TQM)
5、丰田TPM屋
6、设备维修策略与停机关系
7、设备管理考核指标与设定
8、设备管理核心是什么?
9、设备管理的相关方
第二节、故障性质与维修方式的选择
1、选择维修方式的目的
(1)事后维修损失大 (2)定期维修浪费大
(3)预知维修效益佳 (4)各种维修方式的合理比例安排
2.故障性质与维修方式的对应关系
(1)有发展过程的随机故障 (2)无发展过程的随机故障
(3)有发展过程的规则故障 (4)无发展过程的规则故障
(5)课题练习:根据故障性质选择维修方式
3、最佳维修方式的选择
(1)可能性分析 (2)必要性分析
(3)直观判定最佳方式 (4)课题练习:针对某设备拆分选择维修方式
4、设备维修成本
(1)设备维修费用组成 (2)设备故障的潜在成本 (3)维修费用的核算方式
第二篇:设备预防维修管理三大管理方法
第三节、方法一:设备故障递减与事后维修管理
1、什么是设备故障?
2、设备故障类型是如何区分的?
3、颠覆你的认知:设备零故障思维!
4、设备故障的发生发展规律
5、设备故障发生原因探究-丰田5问题法
【行动学习】:某常见设备故障发生原因探究
6、设备故障递减一:长停&重复故障根治
【案例解析】:A3报告的运用
7、设备故障递减二:故障数据分析总结
【案例解析】:月度维修记录分析
【行动学习】:月度汇总报告的作成
第四节、方法二:预防性维修的基本内容和实施方法
1、预防性维修的目的和意义
(1)预防性维修的好处 (2)预防性维修TBM&CBM
2、预期维修计划的实施
(1)预期维修时间的确定 (2)预期维修计划的案例
(3)维修窗口MW (4)维修计划的协调与实施
3、预防点检基础(1 2 3 5 6 9)
(1)一条曲线 (2)二大劣化自然&强制管理 (3)三大根本:清扫&紧固&润滑
(4)五感 (5)六大模块 (6)9大物理特性
4、设备点检的遵守率提升4大法则
(1)路径 (2)项目 (3)基准 (4)现场
5、演练:点检表制作方法演练
6、专业人员的设备点检流程梳理
7、润滑管理专项6步骤管理
步骤0 准备
步骤1 确定供油量和方法
步骤2 改善油供应
步骤3 防止油品变质防止由于润滑不足造成的零部件加速劣化
步骤4 绝对防止泄漏
步骤5 日常检查要点
步骤6 润滑油的润滑性能周期性测试
第五节、方法三:预知维护与可靠性的实施
1、设备维修的评价
(1)赖性指标MTBF (2)维修性指标MTTR (3)计算练习
2、预知维修的工作程序
(1)选择受控设备 (2)确定监测等级 (3)建立预知维修系统
(4)制订监测标准 (5)监测与诊断实施 (6)工作绩效的考核
3、设备的可靠性分析
(1)什么是RCM (2)RCM的产生和发展-维修新观念
(3)RCM分析的输出 (4)RCM的用途及经济效益
4、RCM的原理和分析过程
(1)RCM的基本观点 (2)RCM分析中的7个基本问题
5、监测案例介绍
(1)振动分析
·机械设备的振动分析
·电气设备的振动分析
(2)油品分析
·变速箱油品分析
·液压站油品分析
·变压器油油样分析
(3)红外热成像
·隔热-隔热不良造成的热量损失
·电气设备-连接的热点检测,电气故障和电源线维护
·机械设备-回转窑热点检测和管道监控
(4)非破坏性控制
·磁镜检查
·液体渗透技术
·超声波
·内窥镜检查
第三篇:设备零故障三大分析法
- 方法一:计划保全TPM七步骤分析法
2、计划保全七步骤展开说明
步骤1-设备初始状态分析
(1)初始状态分析
(2) 恢复维护基本条件
(3)故障分析
步骤2-改进以延长组件的使用寿命
(1)消除并防止加速恶化
( 2)应对设备薄弱点的对策
(3)延长设备寿命的对策
步骤3-维护操作的临时标准
(1)建立零部件维护标准以实现零设备故障
(2)建立维护计划的更新以实现零设备故障
步骤4-质量功能的常规检查
(1)评估组件状况对产品质量的影响
(2)更新维护计划以实现产品上零相关缺陷
步骤5-提高检查和维护效率
(1)延长组件寿命以优化维护成本
(2)完善维护系统以优化维护成本
步骤6-条件性维护
(1)发展预测性维护系统(趋势管理)
步骤7-横向拓展
(1)横向拓展
- 中国企业如何推计划保全七步骤
- 计划保全七步骤的案例介绍
- 方法二:WHYWHY分析法
(1)基本技能
(2)解析技能
(3)专业技能
2、如何进行WHY-WHY解析
(1)从应有的型态开始的处理手法
(2)从原理原则开始的处理手法
3、Where分析和Why分析
4、WHY WHY分析2大类
(1)管理层面WHY WHY分析
(2)技术层面WHY WHY分析
5、有效展开“为什么-为什么分析”的10个要点
6、参考事例 找到应该追查原因的问题点
7、某企业烧保险的案例解析
第八节:方法三:设备故障递减常见故障分析工具(FTA为案例 PM QCC)
1、FTA分析概论
(1)FTA分析定义
(2)FTA分析法是用范围
(3)FTA分析产生背景
2. FTA工具分析法
(1)故障树分析的实施步骤
Step 1 准备工作;
Step 2 故障树建造;
Step 3 故障树定性分析;
Step 4 故障树定量分析;
Step 5 故障树分析报告。
(2)FTA分析法常见7大误区
(3)FTA与PM分析法的区别
3. FTA工具推荐
(1)教课书案例练习
4、火柴PM分析案例介绍
5、烧线圈案例在QCC案例应用介绍
第四篇:设备零故障高级应用
第九节:设备管理综合应用
1、设备管理标准构建及案例参考
2、设备检查考核体系构建及案例参考
3、设备管理流程制度建立及案例参考
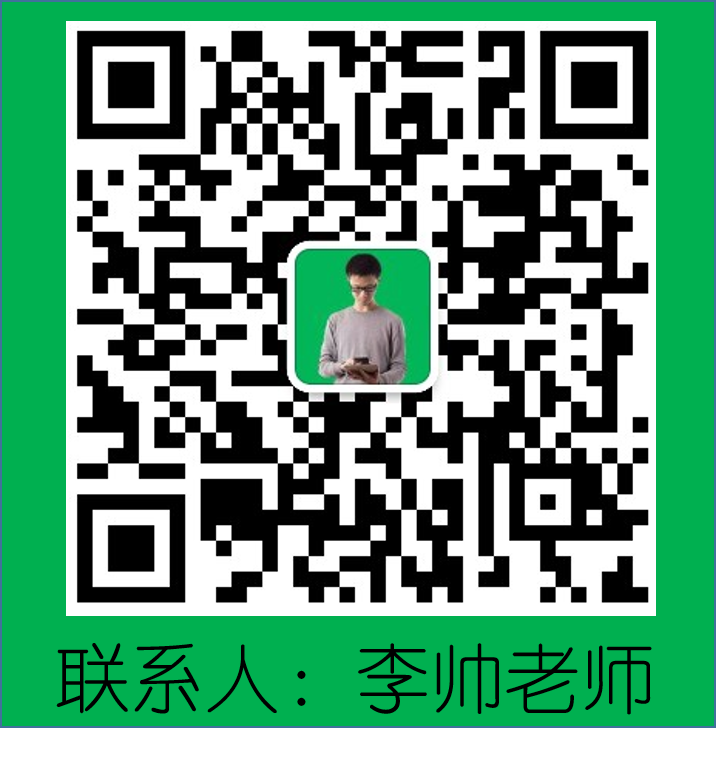