6S管理中如何开展设备管理
发布时间:2016-10-03来源:装备保障管理网交流论坛 编辑:未知

导语
从现场管理讲,设备可同时列为“污染源、清扫困难源、故障源、浪费源、缺陷源和危险源”(以下简称“6源”),因此,做好6S管理,设备管理是一个重要方面。在“6S”管理中,设备管理不只是通过清洁打扫设备,保持设备外观清洁,从更深的层次上讲还要预防、降低和消除设备“6源”。
开展设备管理要从规范设备工作环境,预防和消除“6源”,规范设备现场的日常维护,建立健全规范的设备管理制度,提高职工素质,以及建立考核体制方面开展工作。
规范设备工作环境
根据设备特点和使用要求,建立或配制设备特殊工艺条件要求的环境设施,满足对温度、洁净度等的要求,整理和整顿好设备的工作环境和设备附件,认真区分工作场所要与不要的物品。通过将不需要的物品处理掉,让生产现场和工作场所透明化,增大作业空间,减少碰撞事故,提高工作效率。并把留下有用的东西加以定置、定位,按照使用频率和可视化准则,合理布置摆放,做到规范化、色彩标记化和定置化。
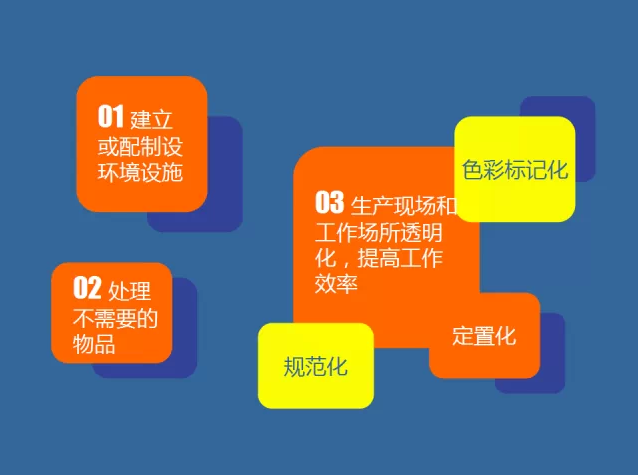
查找和设备有关的“6源”
(1)查污染源。污染源指由设备引起的灰尘、油污、废料、加工材屑等,更深的包括有害气体、有毒液体、电磁辐射、光辐射以及噪声方面的污染。寻找、搜集这些污染源的信息后,通过源头控制、采取防护措施等办法加以解决。
(2)查清扫困难源。清扫困难源指设备难以清扫的部位,包括空间狭窄、没人工作的部位、设备内部深层无法使用清扫工具的部位;污染频繁,无法随时清扫的部位;人员难以接近的区域,如高空、高温、设备高速运转部分等。
(3)查危险源。危险源是指和设备有关的安全事故发生源,安全工作必须消除可能由设备引发的事故和事故苗头,要积极寻找安全隐患并制定策略。对特种设备,要严格按照国家的有关规定和技术标准,由有资质的单位进行定期检查和修理。
(4)查浪费源。浪费源指和设备相关的各种能源浪费,第一类浪费是漏水、漏油、漏电、漏气(汽)以及各种生产用介质等的泄漏(这些泄漏也可污染环境);第二类是“开关”方面的浪费,如人走灯还亮,机器空运转等方面的能源浪费等。要采用各种技术手段做好防漏、堵漏工作。
(5)查故障源。故障源指设备自身故障。要通过日常的统计分析,逐步了解掌握设备故障发生的原因和规律,制定相应的措施以延长设备正常运转时间。
(6)查缺陷源。缺陷源指现有设备不能满足产品质量要求的方面。围绕保障和提高产品质量,寻找影响产品质量的加工环节,并通过对现有的设备进行技术改造和更新来实现。
编制完善的现场工作规范
在编制日常工作规范时,要组织技术骨干,包括设备部门、车间、维护组、一线生产技术骨干选择典型机台、生产线、典型管理过程进行攻关,调查研究、摸清规律、进行试验,通过“选人、选点、选项、选时、选标、选法、选班、选路”,制定适合设备现状的设备操作、清扫、点检、保养和润滑规范,确定工作流程,制定出科学合理的规范,并逐步推广到企业所有机台和管理过程,最终达到台台设备及各个环节都有规范。
提高职工素质
主要指思想和技能两个方面。思想方面,首先要破除“操作工只管操作,不管维修;维修工只管维修,不管操作”的习惯;技术方面,操作工要主动打扫设备卫生和参加设备排故,把设备的点检、保养、润滑结合起来,实现清扫的同时,积极对设备进行检查维护以改善设备状况。设备维护修理人员认真监督、检查、指导使用人员正确使用、维护保养好设备。
对设备管理工作进行量化考核和持续改进
要让企业经营者和职工看到变化和效益,真正调动干部职工的积极性,变“要我开展6S管理,为我要开展6S管理”,有效避免出现一紧、二松、三垮台、四重来的现象。设备进行考核统计指标主要有——规范化作业情况,以及能源消耗、备件消耗、事故率、故障率、维修费用、和设备有关的废品率等。根据统计数据,并以一年为周期,不断制定新的发展目标,实行目标管理。要建立设备主管部门、车间、工段班组、维护组、操作工等多个环节互相协助,交叉的检查考核体系。考核结果要同员工的奖酬、激励和晋升相结合。
从现场管理讲,设备可同时列为“污染源、清扫困难源、故障源、浪费源、缺陷源和危险源”(以下简称“6源”),因此,做好6S管理,设备管理是一个重要方面。在“6S”管理中,设备管理不只是通过清洁打扫设备,保持设备外观清洁,从更深的层次上讲还要预防、降低和消除设备“6源”。
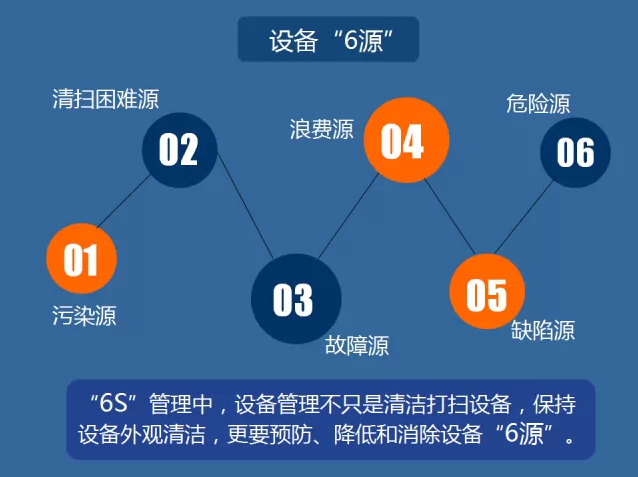
开展设备管理要从规范设备工作环境,预防和消除“6源”,规范设备现场的日常维护,建立健全规范的设备管理制度,提高职工素质,以及建立考核体制方面开展工作。
规范设备工作环境
根据设备特点和使用要求,建立或配制设备特殊工艺条件要求的环境设施,满足对温度、洁净度等的要求,整理和整顿好设备的工作环境和设备附件,认真区分工作场所要与不要的物品。通过将不需要的物品处理掉,让生产现场和工作场所透明化,增大作业空间,减少碰撞事故,提高工作效率。并把留下有用的东西加以定置、定位,按照使用频率和可视化准则,合理布置摆放,做到规范化、色彩标记化和定置化。
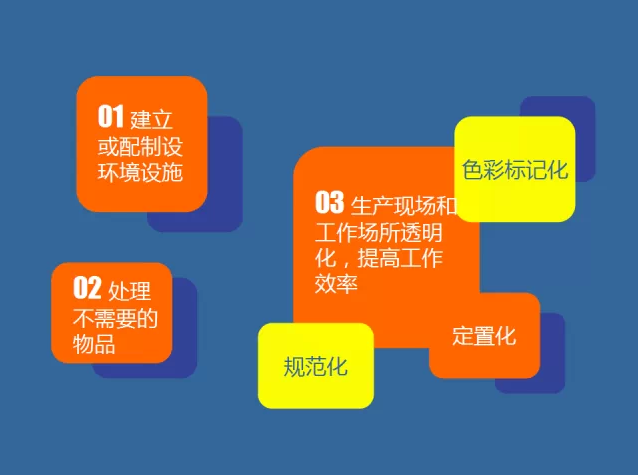
(1)查污染源。污染源指由设备引起的灰尘、油污、废料、加工材屑等,更深的包括有害气体、有毒液体、电磁辐射、光辐射以及噪声方面的污染。寻找、搜集这些污染源的信息后,通过源头控制、采取防护措施等办法加以解决。
(2)查清扫困难源。清扫困难源指设备难以清扫的部位,包括空间狭窄、没人工作的部位、设备内部深层无法使用清扫工具的部位;污染频繁,无法随时清扫的部位;人员难以接近的区域,如高空、高温、设备高速运转部分等。
(3)查危险源。危险源是指和设备有关的安全事故发生源,安全工作必须消除可能由设备引发的事故和事故苗头,要积极寻找安全隐患并制定策略。对特种设备,要严格按照国家的有关规定和技术标准,由有资质的单位进行定期检查和修理。
(4)查浪费源。浪费源指和设备相关的各种能源浪费,第一类浪费是漏水、漏油、漏电、漏气(汽)以及各种生产用介质等的泄漏(这些泄漏也可污染环境);第二类是“开关”方面的浪费,如人走灯还亮,机器空运转等方面的能源浪费等。要采用各种技术手段做好防漏、堵漏工作。
(5)查故障源。故障源指设备自身故障。要通过日常的统计分析,逐步了解掌握设备故障发生的原因和规律,制定相应的措施以延长设备正常运转时间。
(6)查缺陷源。缺陷源指现有设备不能满足产品质量要求的方面。围绕保障和提高产品质量,寻找影响产品质量的加工环节,并通过对现有的设备进行技术改造和更新来实现。
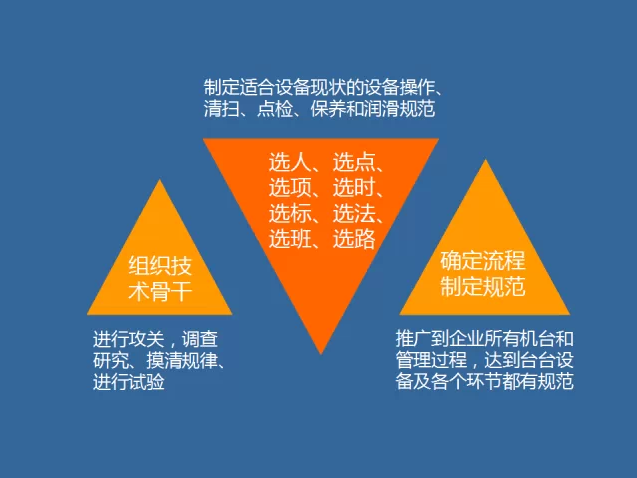
编制完善的现场工作规范
在编制日常工作规范时,要组织技术骨干,包括设备部门、车间、维护组、一线生产技术骨干选择典型机台、生产线、典型管理过程进行攻关,调查研究、摸清规律、进行试验,通过“选人、选点、选项、选时、选标、选法、选班、选路”,制定适合设备现状的设备操作、清扫、点检、保养和润滑规范,确定工作流程,制定出科学合理的规范,并逐步推广到企业所有机台和管理过程,最终达到台台设备及各个环节都有规范。
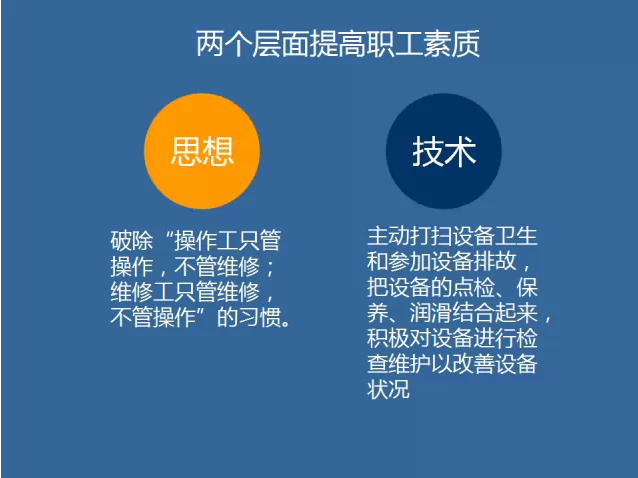
提高职工素质
主要指思想和技能两个方面。思想方面,首先要破除“操作工只管操作,不管维修;维修工只管维修,不管操作”的习惯;技术方面,操作工要主动打扫设备卫生和参加设备排故,把设备的点检、保养、润滑结合起来,实现清扫的同时,积极对设备进行检查维护以改善设备状况。设备维护修理人员认真监督、检查、指导使用人员正确使用、维护保养好设备。
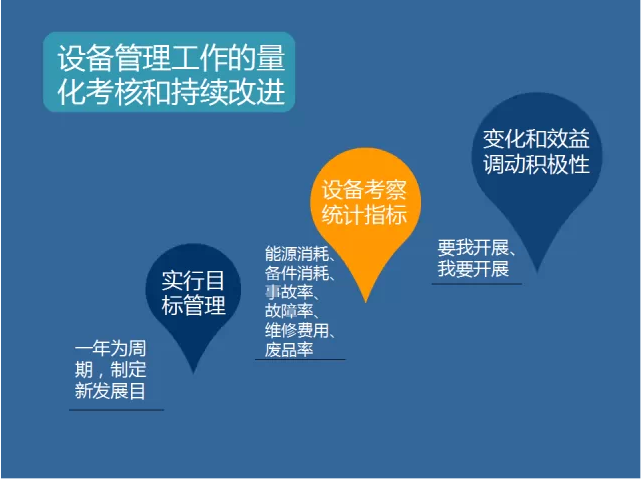
对设备管理工作进行量化考核和持续改进
要让企业经营者和职工看到变化和效益,真正调动干部职工的积极性,变“要我开展6S管理,为我要开展6S管理”,有效避免出现一紧、二松、三垮台、四重来的现象。设备进行考核统计指标主要有——规范化作业情况,以及能源消耗、备件消耗、事故率、故障率、维修费用、和设备有关的废品率等。根据统计数据,并以一年为周期,不断制定新的发展目标,实行目标管理。要建立设备主管部门、车间、工段班组、维护组、操作工等多个环节互相协助,交叉的检查考核体系。考核结果要同员工的奖酬、激励和晋升相结合。